91
Maintenance Guides / Diff Oil Change
« on: 22 October 2006, 13:42:16 »
The Omega utilises a 'sealed for life' rear differential unit mounted on the rear sub-frame assembly.
At high mileage it may be worth changing this oil and, if you have a limited slip diff, its worth changing it every 50K or so miles to ensure the lubricants viscosity properties are good in order to get optimum operation (when iffy the diff can be felt to slip and grab when cornering at low speeds).
This is not a difficult job and is actually a reasonably quick task.
First, you need to jack one of the rear corners and support it on axle stands to allow easier access to the diff.
Once done, you need to disconnect the two ABS sensors from the connectors which are clipped into a set of holders on the floor pan above the diff (see photo below). If you remove them from the clips and ease them down there should be enough cable to allow you to easily free off the two small retaining clips with a small screwdriver and disconnect the connectors.
Now you need to slacken off the two rear diff support bolts (18mm) which can be seen either side of the ABS sensors in the attached pic, don't totally remove them just leave them slack in the housing so its still supporting the diff
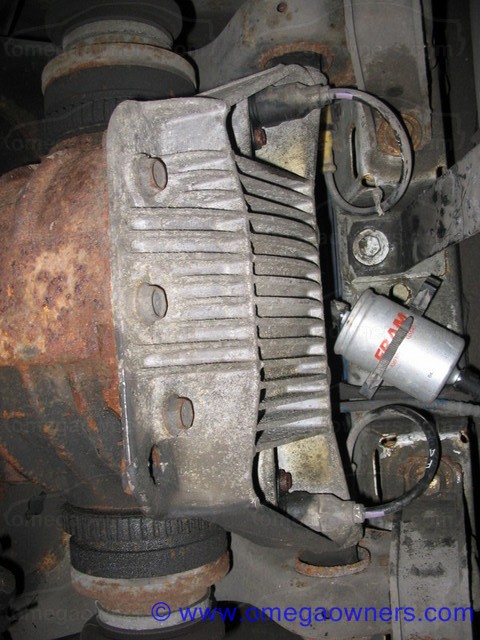
Now undo the rear housing cover bolts (15mm 9 off) slacken off the bottom three a few turns first and then start at the top and work to the bottom, note, oil will start to leak out at this stage hence you need to catch it. Once the oil has drained away, support the rear off the diff on a jack or suitable support and remove the remaining plate and diff support bolts and remove the cover.
Its worth cleaning the cover and ABS sensors well whilst its off and ensure that the diff and plate mating surfaces are clean and oil free ready for assembly.
The following pic shows the internals, this is a shot of the one fitted to my ex plod estate and as you can see, its not an open frame setup due to it being a limited slip unit. The LSD assembly is the large section to the right of the crown wheel.

Once everything is clean, apply some suitable flange sealant (I use Loctite 598 which can be obtained from most places including Halfords) and refit the back plate tightening the bolts in a cross type formation (i.e. top, bottom, left right).
The bolts tightening torques are as follows:
Cover plate 15mm - 60Nm (apply thread-lock)
Diff support bolts 18mm - 90Nm
Once the sealant has had a short time to cure (the loctite above goes off in approx 15 minutes under pressure) the diff can be refilled, in the mean time, re-connect the ABS sensors and ref the connectors into the clips.
The level plug is mounted on the drivers side of the diff and is usually requires a T50 torx bit to remove it (may also be a 8mm allen key fitting). Fill via the level plug until oil starts to run out. The following oils are recommended:
Non LSD - Good quality SAE90 hypoid (approx 1litre required)
LSD - Good quality SAE90 hypoid with LSD additive (i.e. Silkolene BOA90LS available from Opie Oils approx 1.2 litres used)
Refit the level plug and tighten to a torque of 22Nm.
Remove the jack and axle stand and away you go!
Jobs a good one.
At high mileage it may be worth changing this oil and, if you have a limited slip diff, its worth changing it every 50K or so miles to ensure the lubricants viscosity properties are good in order to get optimum operation (when iffy the diff can be felt to slip and grab when cornering at low speeds).
This is not a difficult job and is actually a reasonably quick task.
First, you need to jack one of the rear corners and support it on axle stands to allow easier access to the diff.
Once done, you need to disconnect the two ABS sensors from the connectors which are clipped into a set of holders on the floor pan above the diff (see photo below). If you remove them from the clips and ease them down there should be enough cable to allow you to easily free off the two small retaining clips with a small screwdriver and disconnect the connectors.
Now you need to slacken off the two rear diff support bolts (18mm) which can be seen either side of the ABS sensors in the attached pic, don't totally remove them just leave them slack in the housing so its still supporting the diff
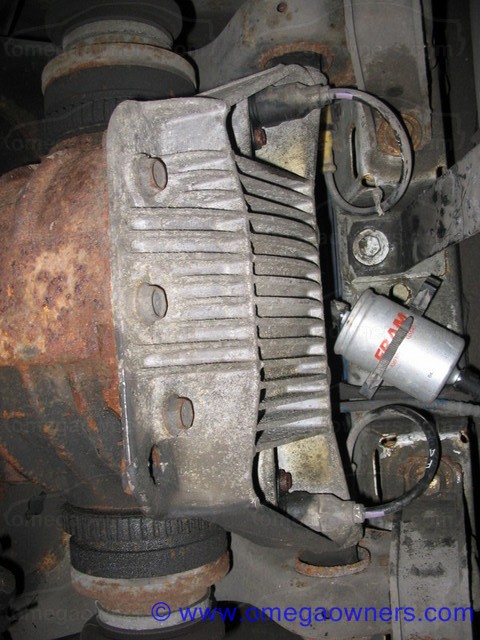
Now undo the rear housing cover bolts (15mm 9 off) slacken off the bottom three a few turns first and then start at the top and work to the bottom, note, oil will start to leak out at this stage hence you need to catch it. Once the oil has drained away, support the rear off the diff on a jack or suitable support and remove the remaining plate and diff support bolts and remove the cover.
Its worth cleaning the cover and ABS sensors well whilst its off and ensure that the diff and plate mating surfaces are clean and oil free ready for assembly.
The following pic shows the internals, this is a shot of the one fitted to my ex plod estate and as you can see, its not an open frame setup due to it being a limited slip unit. The LSD assembly is the large section to the right of the crown wheel.

Once everything is clean, apply some suitable flange sealant (I use Loctite 598 which can be obtained from most places including Halfords) and refit the back plate tightening the bolts in a cross type formation (i.e. top, bottom, left right).
The bolts tightening torques are as follows:
Cover plate 15mm - 60Nm (apply thread-lock)
Diff support bolts 18mm - 90Nm
Once the sealant has had a short time to cure (the loctite above goes off in approx 15 minutes under pressure) the diff can be refilled, in the mean time, re-connect the ABS sensors and ref the connectors into the clips.
The level plug is mounted on the drivers side of the diff and is usually requires a T50 torx bit to remove it (may also be a 8mm allen key fitting). Fill via the level plug until oil starts to run out. The following oils are recommended:
Non LSD - Good quality SAE90 hypoid (approx 1litre required)
LSD - Good quality SAE90 hypoid with LSD additive (i.e. Silkolene BOA90LS available from Opie Oils approx 1.2 litres used)
Refit the level plug and tighten to a torque of 22Nm.
Remove the jack and axle stand and away you go!
Jobs a good one.